Sandler Showcases Nonwovens for Office Use
At this year’s Orgatec exhibition for office design and furnishing, Sandler showcased its nonwovens under the motto “The textile office.” Sandler’s nonwoven panels are designed to offer acoustical benefits in workplaces with a high noise level. Applications for these polyester nonwovens include acoustically efficient back walls to office cabinets, suspended ceilings or partition walls. These create good conversational acoustics and a pleasant atmosphere. According to executives, the company works with with well-known manufacturers of office materials to perfect sound the sound insulating properties of its nonwovens acoustic nonwovens, which can be enhanced with printing and embossing motifs. Thee materials also dampen machine noise in industrial environments. In addition to acoustical products, Sandler’s nonwovens are used as an upholstery layer placed directly under the cover fabric of office chairs, providing long-lasting seating comfort. Owing to its high recovery rate, the high-quality material retains its shape—no matter how many times a day the user gets up and sit down again. Air-permeable and breathable, Sandler nonwovens also contribute to an optimal micro-climate of the seat, for pleasant and productive working environmenta, in summer and winter.
http://www.nonwovens-industry.com/issues/0115/view_breaking-news/sandler-showcases-nonwovens-for-office-use/
Nonwovens in Automotives
While nonwovens have penetrated many areas of the car, there is still room for expansion in this growing market.
The average age of the North American automotive fleet is the lowest it’s been in years; manufacturing in general is ramping up; and car makers are looking for ways to make their vehicles lighter and more fuel efficient. All of these factors are adding up to make it a great time to be a nonwovens manufacturer targeting the automotives market.
“Right now, the automotives market is on the upturn,” explains Gale Shipley, automotive sales manager at nonwovens maker Dalco Nonwovens,” which makes investments in new equipment easier to justify due to the increased demand from the market. All manufacturers, however, remain cautious due to the downturn in 2008-2009.”
Shipley adds that she has seen a substantial increase in the amount of nonwovens going into vehicles, driven by the need for reducing cost without compromising quality. In this conversion, North America has lagged Europe where green-driven needs like fuel efficiency and recyclability have been regulated by the governments at a much earlier timeframe.
According to data recently released by EDANA, the European Disposables and Nonwovens Association, nonwovens offer many advantages in the car. Because nonwovens are typically 15-30% lighter than competing materials, they can make a car more than two kilograms lighter. Meanwhile, the average passenger car using nonwovens can save 55 kilograms of CO2 over the life of the car. Cars using nonwovens in all possible applications, from insulation to lining, have a benefit of more than 30% less impact on the environment.
Not a Drag
One area where Dalco is seeing more interest for nonwovens is in underbody shields and belly pans, installed underneath the vehicle to reduce air drag and improve gas mileage. In recent years, the percentage of North American cars that have these products has increased approximately 30%, driven by government mandates to increase miles per gallon averages by 2025.
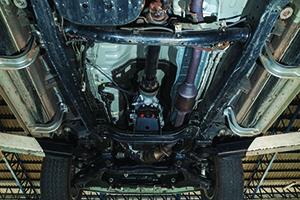
Nonwovens are increasingly finding a spot underneat the car.
“This is one of the small pockets of innovation that have come about in the face of the need for better fuel efficiency, Shipley says.” “Auto makers know their targets, with regard to mpg and are examining different areas to achieve them.”
Another area where nonwovens are helping automotive makers meet fuel standards are in light weighting. Here, executives say that manufacturers look at grams, not kilograms, meaning that any weight reduction, no matter how seemingly insignificant, is considered.
“If a car maker can save a few grams here or there, it can mean a lot,” says John Bradburn, manager of waste reduction at General Motors. “Whenever you build a lot of vehicles like we do, anything counts. Any weight reduction can get the attention of engineers and designers.”
While changing material to nonwovens in any area of the car can be challenging as nonwoven grades become lighter weight in the future, he envisions more acceptance of nonwovens in even more areas of the car. Also, benefitting nonwovens is their ability to accept different grades of resin, including recycled goods or other sustainable materials.
Texel, Saint-Elzear, Quebec, Canada has made strides in automotives with ThermoFit nonwovens. This substrate features a monolayer construction with a single black layer of 40% polypropylene and 60% polyester. This substrate is stabilized which the company says prevents any shrinkage during the preheating process. ThermoFit is designed to offer elongation and stiffness properties, which are ideal for wheel well liners and underbodies.
Marc-André Drouin, business unit manager, automotives, for Texel, says that nonwovens, when used in acoustics, can offer a significant weight reduction compared to injection plastic. Because the density is not 100% polypropylene or polyester, the product is made using a sandwich construction and the middle is soft, saving up to 30% in weight reduction. “You need a lot less material so they are saving weight and they are saving money,” he says.
“Each OEM has a target of weight reduction. The price to save weight may increase as they get closer to launching the car, they may be willing to pay more for some part that reduces weight.”
Texel recently invested $15 million in a new Dilo production line. This new equipment is allowing Texel to increase its production capacities by more than seven metric tons of transformed fibers per year and will allow for the manufacturing of products with a width of 5.25 meters. This new line is equipped with an inline oven and calendar rolls, which will also allow stabilizing and increasing the density of the moldable substrate.
Dalco, meanwhile, makes needlepunch products, sometimes in multilayer formations, in weights that range from 70-80gsm to 2000 gsm. Shipley says that while weight reduction is important, the ultimate goal is increased fuel efficiency.
“Regardless of weight addition, the end goal appears to be driven by improved mileage averages. We see non-glass fiber underbody shield material ranging from low weights of 800-900 gsm to substantially higher at 2000 gsm. Innovation will drive this market as OEM’s better understand the requirements,” Shipley explains.
In addition to reducing weight and fuel usage, nonwovens are also offering opportunities for cost savings. One material helping this cause is regenerated polyester, used in a number of moldable nonwoven products. In fact, Shipley says that regenerated materials, having lower melting points than virgin polyester, mold better while bringing the cost down. As the demand for regenerated polyester is increasing, manufacturers have fine-tuned their processes to guarantee physical parameters such as shrinkage and tenacity, etc.
Keeping Up Appearances
The challenge with using regenerated polyester, however, is color matching or visual harmony, so automakers are relying on a blend of fibers combining virgin and regenerated products or using 100% virgin polyester, depending on where the material is located in the vehicle.
“Molders are using mixed color regenerated polyester on the non-visible, or the moldable substrate side, to reduce cost while using virgin material or a matched fiber blend on the visible-side,” she says. “The other choice is to have a homogenous product with bico or polypropylene fiber for moldability.”
“At Dalco we are seeing both,” Shipley says. “Some customers want a color-matched face with less expensive mix in the substrate and others want homogenous blends in bico mixtures.”
“As for entry into the OEM or Tier 1 acceptance arena, if the product is higher performing with potential cost reduction, it is easier to get buy-in on the product. If it is an equivalent trade on pricing and quality, it’s much more difficult,” Shipley adds. “There, however, is a gray zone where there is improved performance and equivalent price that is easier to sell but still difficult to get entry into the industry, especially with regard to refreshed vehicles, due to PPAP and lab package costs.”
Where Next?
Vamsi Jasti, R&D Engineer, Johnson Controls, a manufacturer of automotive components for major automotive makers, reports that nonwovens usage in seating applications has lagged other areas like carpets and headliners because it can be a challenge to get car makers to swap in new materials.
“We believe that current products are optimized for cost and performance,” he says. “It’s not easy to replace an existing component, especially in the seating area.”
Adding to this challenge is a perception among car makers that nonwovens are lower cost, and lower quality, than other materials.
”Automotive products are functionally and cost driven,” Jasti adds. “It’s really a challenge for the nonwovens to conquer the new areas. Nonwovens are more like a commodity and are optimized for their cost. Stretch, residual set, elongation and abrasion resistance are some of the property-related issues that prevent the use of nonwovens in some areas of seating.”
Even as nonwovens struggle to penetrate new areas, many producers remain bullish about the market. One of the companies is German nonwovens Tenowo. The company, which is in the midst of a major, multicontinent investment program, credits much of its growth in recent years to the automotives market. The company currently offers eight different manufacturing technologies that are used in automotives, giving it the advantage to meet the full spectrum of needs in the market.
“Nonwovens offer high performance associated with reasonable economics” rather than “low cost fabrics,” says Detlev Kappel, director of sales. “The trend to substitute ‘classical’ textiles such as circular or warp knits for interior decorative apps still continues. We find highly engineered nonwovens in headliners, car seats, trunk, door panels, floor carpet sandwiches are still more cost effective compared to other textiles or material systems but at higher price level than some commodity types.”
The entry barrier into the automotive world is still often underestimated. To stay healthy you need to be a global partner, willing to take high risks, able to live with low margins and continuous price pressures and offer excellent sales network and service.
“Every technology has its own pros and cons, so it’s perfect if you can offer all of them to your customers on a global basis,” he adds.
Looking forward, Kappel says he sees acoustical applications to be the main growth driver for nonwovens in automotives both in developed and developing regions globally. Tenowo is targeting this area with AFR scrims (air flow resistance scrims), a new product that allows customers to reduce the weight of their parts and simultaneously maintain the acoustical performance.
The company also has new stitchbonded products to be used in car seats under genuine and PUR leather and new generational spunlace products for injection molding and superior acoustic applications.
GM’s Focus on Sustainability
GM’s Bradburn said that all of manufacturing can learn from efforts being made in the automotives market when it comes to waste reduction, green practices, energy conservation and other sustainability efforts. “This started for us about 20 years ago, when we realized there were significant opportunities to reduce waste and increase revenues. It’s been a long road but it’s been a good one.”
In October, GM announced that 11 more of its facilities have achieved landfill-free status bringing the running total to 122 manufacturing and non-manufacturing operations spanning Asia, Europe, and South and North America that recycle, reuse or convert to energy all waste from daily operations.
“Our landfill-free movement is part of our culture of continuous improvement embraced by teams globally,” says Jim DeLuca, GM executive vice president of Global Manufacturing. “Not only does it make our operations more efficient and help conserve vital resources, but we’re able to reinvest the money we get from recycling into future vehicles for our customers.”
The addition of these 11 facilities to landfill-free status helps GM avoid more than 600,000 metric tons of CO2-equivalent emissions. This is comparable to the greenhouse gas benefit of 15 million tree seedlings grown for 10 years.
“Our ultimate goal is not to generate any waste at all,” says Bradburn. “Until then, we do everything we can to ensure it doesn’t end up in the ground. From connecting our suppliers on special recycling projects to reusing packaging, we apply lessons learned across all of
our operations to broaden the positive impact.”
A strong network of recycling partners and suppliers helps facilities achieve their goals. Localizing the supply chain strengthens the business case and reduces the overall carbon footprint.
http://www.nonwovens-industry.com/issues/1214/view_features/nonwovens-in-automotives/
Pocket sprung shoe uses needlepunch nonwovens
Coil technology provides cushioning, springy sensation
By Karen McIntyre, editor
Using nonwovens technology normally found in a mattress, a group of U.K. researchers have developed a casual shoe featuring a distinctive springy sensation underfoot. Spinguru causual shoes are now featured on the Kickstart crowdfunding site.
Each pair of the Springuru has 34 pocket springs, lined with 100 gram needlepunch nonwoven material, built into the EVA. This allows the shoe to provide great cushioning, support and comfort and an unbelievably springy sensation.
The shoes borrow technology developed by mattress manufacturer Harrison Spinks to develop a process to produce micropackets. The conical springs are precision placed, pre-compressed in their fabric pockets by an ultrasonic welding process. While mattress springs usually use a standard needlepunch or spunbond material around them, the shoe applications required a 100 gram needlepunch because it needed to be strong and soft at the same time. “We started by taking sneakers apart and adding coils,” explains company spokesman Darren Marcangelo. “We immediately noticed a big difference.” What followed was a two-year collaboration with University of Central Lancashire building on the technology. Professor Jim Richards, professor of biomechanics at the university played a key role in the development of this concept. “While other shoes achieve a cushioning or damping effect by using EVA in the midsole, the Springuru midsole construction deploys a spring and damper arrangement, much like you find in a car suspension system,” he says. “This is an efficient arrangement that can lead to improved loading rates and reduced impact forces.”
According to Marcangelo, who also works at Harrison Spinks, the technology behind Springuru has already been licensed to an athletic shoe company, and he and his partners are looking to commercialize a casual shoe under the Springuru brand name. This laceless upper is made of a stretch ballistic nylon. It’s tough, breathable and custom conforms for a perfect fit. The sole design is a nod to the mattress heritage of the pocket spring component.
Targeting 25-40-year-old men and women, the Springuru hopes to eventually sell the shoes at select retailers. For now, however, the company is hoping that its crowdfunding campaign on Kickstarter achieves its fundraising goal of by the end of October, which will allow production to begin in January.
http://www.nonwovens-industry.com/contents/view_online-exclusives/2014-10-09/pocket-sprung-shoe-uses-needlepunch-nonwovens/
Russian Nonwovens Industry Ready for Breakthrough
The Russian nonwovens industry is growing, reflected by the increasing volume of domestic production as well as the launch of new investment projects.
By Eugene Gerden, Contributing Writer
The Russian nonwovens industry is growing, reflected by the increasing volume of domestic production as well as the launch of new investment projects. During the period of 2007-2012 the volume of nonwovens production in Russia increased by 7.6% to 2.4 billion square meters. The production figures for the 10 months of the current year have not been announced, however, according to predictions of local analysts, this year the market continues to grow and is expected to reach 2.6 billion square meters. At the same time there is also a possibility that by 2017-2018 the market could reach three billion square meters.
In recent years, Russian nonwovens production has become competitive not only in the domestic, but also global market, with some Russian products becoming best sellers in some market segments. For example, currently Russian companies are among the world leaders in narrow technical fabrics, which are used in the manufacture of car seat belts, as well as lifting, hiking and climbing belts. In terms of structure of production, the majority of production accounts for nonwovens used as a base for polymer coatings including linoleum, table oil cloths, rolled roofing material, wallpaper and cleaning materials among others. Second place is occupied by geotextiles and agrotextiles while sitting in third position are heat and noise insulation materials for cars, pipelines, industrial facilities and residential buildings.
Finally, the share of filtering, medical and sanitary products is estimated at only 10% of the market. The production of nonwovens for medical use remains small and uncommon in Russia. This is reflected by the fact that at present Russia has only one producer of such products and in particular Kondrovskaya paper mill, which is located in the Kaluga region and specializes in the manufacture of disposable medical clothes and accessories, based on three-layer nonwoven fabric.
According to Alexander Markov, CEO of Regent Nonwoven Materials, one of Russia’s leading producers of nonwovens, in terms of consumption, about 29% of all nonwovens produced in Russia, are consumed by local construction industry; 24% by the country’s agricultural sector; 22% by the industry of sanitary and hygiene products; 16% by industrial production; and 9% by the Russian medical industry. Markov’s prediction is that during the next several years the market will continue to grow, with the biggest growth expected to come from women’s and children’s hygiene products.
However, despite big prospects, certain problems will prevent rapid development of the market. Noncompetitive prices for raw materials and in particular for polypropylene is expected to be one of them. This will result in the underutilization of many existing production lines, and even those operated by foreign investors. Despite the existing production capacities in Russia, many foreign players prefer to launch production abroad with further imports to Russia. This strategy is considered more profitable by some investors due to Russia’s recent WTO accession, import duties on imports of many industries finished products, and a significant decline in raw materials production. At present custom duty on the imports of finished products to Russia and in particular for baby diapers and sanitary products is set at 5%. At the same time import duties on the basic raw materials are at the level of 9.1%, which creates conditions more favorable for a steady flow of imports to the country.
According to Markov, many Russian nonwovens producers are experiencing serious losses due to the high cost of raw materials. He says the raw material situation in Russia makes it difficult to remain profitable due to high cost of polypropylene, which is currently estimated at 40,000 – 50,000 rubles per ton (US$1330-1666). At the same time among the other industry problems is also the dependence on the imports of cotton, as well as the lack of domestic production of viscose, chemical fibers and new generations of man-made yarns.
Due to this, many of Russia’s leading producers of nonwovens have repeatedly appealed to the Russian government to impose restrictions on the exports of fine-wooled merino and raw hide to the country, as well as to design a set of measures aimed at developing a raw materials base for the national textile industry, mainly through the provision of cheap loans for the purchase of domestic raw materials. Dmitry Finer is commercial director of Edelweiss, one of the leading manufacturers of nonwoven polyester materials in the market of former Soviet states. “We find it difficult to compete with foreign rivals in terms of price, although the quality of our products is not inferior to the quality of its foreign analogues, produced by German or Chinese companies,” he says. “Due to the fact that Chinese manufacturers receive state aid they can offer lower prices for their products.”
In the meantime, local producers also believe that state aid can be provided not only through direct subsidies and financial support, but also through the development of cooperation among the producers and consumers as well as state promotion using the same model as in some EU countries and in particular Germany. Despite the existence of numerous problems, in recent years the investment attractiveness of the Russian nonwovens industry has significantly increased, as seen by a number of large-scale investments scheduled for implementation by domestic and foreign investors in Russia in coming years. One of these projects will be officially launched by the end of the current year and involves the commissioning of a new plant for the production of nonwovens in the Troitsky District of Moscow. The project is implemented by Russia’s Regent Nonwoven Materials and involves building a plant on the total area of 7400 square meters. The new plant will specialize in the production of synthetic spunbond nonwovens. The new plant will have the capacity to produce 1500 tons of nonwoven materials per year and is expected to be one of the largest of its kind in Russia. Russia’s petrochemical giant Nizhnekamskneftekhim has announced plans to increase production of nonwovens.
On April 3, 2013 became the owner of 100% of the shares of CJSC Polymatiz, a Russian producer of nonwovens. Currently the enterprise produces 700 tons of nonwoven materials per year, however there is a possibility that during the next several years its capacities will be significantly increased. Finally, a new large plant for the production of polyester fiber and a new generation of nonwovens will be built in Russia this year by the local company CJSC Kotovsky Nonwovens Plant, one of Russia’s largest producers of nonwovens. The new plant is expected to be built in Russia’s Tambov region and will require a total volume of investments of more than 2 billion rubles (US$60 million). The capacity of the plant will be 210,000 tons of polyester fiber per year as well as 20,000 tons of new generation multi-layer nonwoven materials.
The plant is expected to be operating by 2015. The company says there plans are to focus on the production of innovative nonwoven products for the medical field and include materials based on layers obtained by spunbond and meltblown technologies.
http://www.nonwovens-industry.com/issues/2013-12-01/view_features/russian-nonwovens-industry-ready-for-breakthrough/